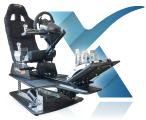
The most recent update is on top so it's new to old
Update 30.11.2012
Since my project is finished it was time to move it to the finished project section.
Because there's quite some off topic discussion in this topic which could confuse people reading it for inspiration I decided to create a new topic instead of moving this one.
The new topic can be found here: viewtopic.php?f=36&t=617
Any new discussions or questions about this project can be posted there, this one get's a padlock

Thx for all your comments, replies and help!!!!!
Update 26.11.2012
A few days ago I've finally finished my build

The last remaining thing left was to create a decent electronics board and cool the PSU's with more silent fans:
With this I'm calling this project DONE! (for now at least

Update 16.10.2012
Shot another video last night. Still messing with the profile, but it's getting there

Update 02.10.2012
Today I finally got to testing my new motors

Been busy with some home improvement, but most of that's finished so it was time for some fun work.
They move like h#ll that's for sure! But I do need to retweak my profile though.
For those interested in the settings:
PID: 6/5 - 13/8 - 3/2
PID period: 10ms
Integral limit: 1000
Feedback deadzone: 2
Max duty cycle: 450
Max acc.: 450
Brake duration: 0
Max current: 30A
Max duty cycle while feedback is out of range: 450
Anyway here's a short 2 min video of the motors in action, as mentioned the profile needs tweaking and I will make a new video in better light conditions soon:
Update 07.09.2012
Shot some quick photo's of the rebuild sim today. Will do a decent photoshoot when it's all finished (with a proper flash set).
As you can see I added some skateboard griptape to prevent skidding and damage to the paint. And also added a few aluminum strips where the feet of the pedal base slide over whilst adjusting it.
Still waiting for my new PSU's so didn't get to using it yet

Update 26.08.2012
the last few days I've spend some time on making my new motor mounts.
New against old:
Mounted underneath the platform:
So far I've discovered onyl 2 minor downsides to the motors:
1) They don't stick to their position if you take the power off (my wiper motors did), most likely due to the gear ratio being different. No major problem though, this just means I have to start the profiler before stepping onto the sim.
2) They kill power supplies

http://www.ebay.nl/itm/12V-45A-600W-Swi ... 5ae92a13a5
I didn't get to testing the advantages of the new motors yet since my test ended prematurely

Update 02.08.2012
Back again with almost the same picture as the last one. Can you spot the differences?

I also added 8 rubber feet underneath the bottom platform
And decided to add the extra springs I had to the pivot so I have a bit more adjustability. With a single spring on each corner I had to expand them as far as possible so I had no room to play with different tensions. With the double springs I can test some different variations to see what works best.
Update 26.07.2012
Today, eventhough it's our holiday and it's bloody hot overhere

The complete disassembly took me only half an hour and the tools on the photo are all the tools needed.
Update 19.07.2012
Today my new motors arrived.
What a difference compared to the wipers

Update 12.07.2012
A short video of a friend of mine having a first go on my sim. The squeeky noise is one of the motors that needs some greasing

The motion profile needs some work.
Update 09.07.2012
Yet another update with only a single image, but once again a pretty important one

First of all here's a picture of my electronics board:
In a later stage the panel will be painted black and will be mounted in a box with a plexiglass top.
And for the important part without pics: It's allive!!!
A few days ago I got my sim up and running!
I had some problems with one of the shaft couplers that kept loosening (the same side as the broken thread) and still have to fasten it once in a while, but finally can drive around and experiment with the software.
Update 13.06.2012
Not really an update with a lot of photos but one with a lot of work behind it.
Have been working on mounting all parts together and since this was mostly "drill a hole / hit a T-nut into the hole / fasten a bolt" this wasn't really worth taking pictures of.
I did however shoot a short movie with one motor quickly connected to an old PC PSU (so no JRK's etc. yet).
Update 02.06.2012
Found some time to do some work today:
Since a playseat isn't build for people who are almost 2m tall I wasn't really happy with the wheel positioning. It was a bit too close for my likings or ended up being too high.
To solve this problem I firtst cut of the piece of plastic sticking out of the wheel mount towards the driver.
This leaves an ugly edge, but as you can see in the next pictures this will be covered by my new mounting plate for which I also took the sequential shifter into account.
And here it is remounted on the seat, now the wheel is about 10cm further away and a lot better positioned.
Of course the wood will be painted black later on.
On the last two pictures you can also see I've allready cut a plank for my pedals, they will be mountable in 2 ways. On the right for driving with clutch and right foot braking, on the left for driving sequential with left foot braking. But more on this later.
Update 16.05.2012
Here's the better pic of the pivot I promissed:
And I couldn't resist stacking the parts together to get a general idea of the end result:
I was afraid the springs would be too strong, but the way they are currently mounted (no spring load/tension when the platform is balanced) and without driver (which eventually brings the center of gravity more towards the rear) the platform slightly tilts forward and only a bit of force has to be applied to tilt it sideways.
So I reckon they aren't too strong after all since I will have to increase the spring tension especially when a driver adds another 90kg to the weight :cheers:
Update 15.05.2012
Last weekend a friend of mine welded my pivot.
Here's what it looked like after welding and cleaning of the paint and exces rust:
After the paint job together with all the other parts:
Unfortunately they send me 2 pink springs instead of all red ones, but new red ones are on their way!
And after assembling:
It was getting dark, hence the crappy picture, but I'll try to take better ones together with the next update.
The best spots for the spring will have to be determined after building the entire rig, for now I placed them at the end because this was the easiest.
They are pretty strong so I reckon eventually they will have to stay pretty close to the pivot.
Update 08.05.2012
Finally got to do some more work on my build the past few days.
First of all I printed a template for my platforms on 12 A3 sheets, glued them together and cut them:
After drawing the top platform onto my plywood I could cut of the extruding piece which results in the base shape for the bottom plaform:
And finally after cutting them with the hacksaw, rounding the edges with my router and some sanding here's the result:
Update 25.04.2012
Just mounted the other motor assembly as well:
Now you can see what I meant with "mirror mounting" the motors, this way they both stick to the back, imho better than one sticking forward
Update 24.04.2012
Some more progress on the motor assemblies, finishes one of them as far as possible:
First of all, the motor mounts:

Eventhough the motors run slightly faster in one direction than in the other I took the risk of "mirror mounting" them because this simply looks better.
Next I assembled one of the motors:
(Don't mind the greasy fingers, I'll clean those of once finished

And finally mounted it all together:
Must say I'm very pleased with the result

Update 21.04.2012
Last week I've spend a few hours on cleaning:
And painting the motors:
Unfortunately the silver paint (which I expected to be more greyish looking at the spray can's cap) shows all surface irregularities of the gear housing and the silver and the primer didn't really like eachother and there are a few minor blatters in the coat, but not disturbing enough to sand them down again

Update 11.04.2012
Ever wondered what a disassembled wiper motor looks like?
Here you go:
On the photo you can clearly see the third carbon brush for the slow speed on the "pcb" (the 2 opposite of eachother are low speed, the one under an angle is for high speed).
I'm going to leave the ones for slow speed out so I have some spare carbon-brushes and one less wire (next to that it reduces drag slightly, being neglectable though I reckon).
There also are 3 brush/sliding contacts in the plastic part (not visible on the photo) which make contact between the center 3 pins and the axle gear. 2 of them aren't connected and one of them is for grounding the axle. These I'm going to take out as well since they are useless to me and cause unnecessary friction as well (also neglectable but why keep them if they are useless).
At first I thought I had 2 identical motors and opened up one to check if they had metal gears and they did.
Later I discovered the housings where a little different as well as the rpm. Today I wanted to disassemble one to see if they are easy to clean so I took the other one and unfortunately it is indeed different and has a plastic gear and less beefy rotor

Luckily I most likely found someone who has another one of the first type.
Update 10.04.2012
Tonight I found some time (very busy with all kinds of stuff except for my sim :thbd: ) to finish my bearing supports:
Once again sorry for the crappy pictures but I just don't feel like taking out the DSLR for them

Update 31.03.2012
Last week my aluminum finally arrived

And after a lot of drilling (3x per hole -> 2,5mm -> 5,5mm -> 8,5mm), countersinking (2x per hole -> both sides), rounding corners and sanding part of it results in:
The shorter pieces will be mounted on steel plates:
And the longer pieces will be mounted onto the above:
I have 2 of these parts but only mounted one for now because eventually my u-joint will be welded in between the two and the steel parts will be painted black after that.
All in all this results in an adjustable pivot for balancing purposes.
The unused aluminum is for the next step: The motor mounts
Update 15.03.2012
Since my pivot will be adjustable (in steps of approx. 16mm) I decided to take my chances on my estimates.
Last night I determined the approx. balance point of the seat incl. myself and a MS wireless xbox wheel as well as with the estimated weights, they only differ approx. 5cm so if my estimates turn out to be a few Kg off this will only result in the balance point shifting slightly.
Here's my final design for the platform (the dashed red line represents the bottom platform):
I used Deriy's motor mounting point distance
Theoretically, combined with my 5cm motor arm travel (10cm total) this results in a max platform angle of:
Pitch: +7.12 and -7.12° = 14.24° total
Roll: +9.46 and -9.46 = 18.92° total
Which should be enough to make me seasick

Edit: Rotation sample
Update 14.03.2012
Lol, this project is slowly getting out of hand

Since I have to wait for my m8 to weld the u-joint I have too much time to think of new stuff

I found a cheap aluminum supplier for my new motor mounts (gonna add an extra mount with a bearing for moving the axle load from the motor to this point) and because they where so cheap I also ordered some extra aluminum for making my pivot adjustable. (you'll see when I get to that).
Also ordered some warnex today which is speaker paint for structure painting for my platforms.
On the parts of the platform where you can put your feet I'll place skateboard griptape to prevent the paint from wearing and people from skidding off

Next to that I decided to make a seperate box with the psu's, usb hub, jrk's in it (with spare room for a 3d jrk/psu to be 3DOF proof

I'll keep you posted of course! Don't have as much time for building as I have for thinking about new stuff, but you'll see the updates when I made some progress.
Now on to the reason why I came here to make this post:
Since I've tried to gather the Fanatec CSR Wheel, CSR Elite pedals and shifter weight, but unfortunately didn't get a single reply on different forums I'm active on I decided to guess and hope that you guys would like to state if you think my guesses could be correct.
The package weights are the following:
• CSR Wheel: 5,6kg
• CSR Elite pedals: 7kg
• CSR Shifter set: 5,6kg
Since the wheel has a PSU, the shifter has 3 parts of which 2 are used at the same time and the boxes will have some weight as well my estimates are:
• CSR Wheel: 3kg
• CSR Elite pedals: 5kg
• CSR single Shifter with mount: 3kg
Gonna determine my balance point based on those weights and create my platforms accordingly and since my pivot will be adjustable hope this will turn out right, but if any of you have any thoughts on my estimates: Please share them!
Update 10.03.2012
Made the pot mounts today:
Also wanted to build a test setup with a single motor on a plank, but ran into a problem during the mounting.
Due to the construction of my motor arm it can't make a full rotation because the head of the bold hits the motor housing.
Luckilly I noticed this before powering up the motors :cheers:
Back to the drawing board (as a figure of speech

Update 09.03.2012
Took me more time than I hoped for, but managed to go from this:
To this (white pads are thermal conductive tape):
To this:
Together with some decent airflow this should do the trick of keeping them cool
Update 07.03.2012
Just finished the pot pivot arms and assembled the complete motor arms:
Update 06.03.2012
Started making some pivot arms for the pots tonight.
Here's a few pictures during the routing (damn I want a CNC router :yes:):
And here's the rough finished product (needs sanding):
Sorry for the somewhat crappy pics

And now it's time to give the wife some attention

Update 04.03.2012
Yesterday a friend of mine dropped of some old car parts

I'm very happy with the uni joint of the drive shaft:
It has absolutely no play and moves very smooth :thbup: (needs a bit of cleaning and painting though

It's the wiper motors that concern me:
The wormwheel as well as the gear are alll metal, but the housing cover is plastic.
Update 24.02.2012
The JRK's arrived yesterday


Finally I can start doing some minor work: Creating the heatsinks for them.
I am planning on modifying an existing CPU heatsink into 2 heatsinks for the JRK's that cover all chips on them.
This requires some downsizing and routing to the base of the heatsink because of the chip height differences.
Luckily I have a column drill/router (I'd rather hava a CNC router, but this will do

Edit:
Also did a redesign on the plaform:
Top platform:
Bottom platform:
Inspired by the body shape of an F1 car (a bit that is) and compared to the first design it's easier to create a "cloth" cover between the bottom and top platform for hiding the construction (Deriy style).
Still need the weight of the Fanatec CSR wheel, CSR Elite pedals and CSR shifter to be able to determine the balance point and thus the motor mounting points though. Trying hard to figure these out.
Update 15.02.2012
Just a tiny little status update: Managed to geld hold of two brand new Pololu JRK 12V12's for $ 140,- including shipping today

So now, when YoBuddy's package arrives, I have electronics for controlling 4 motors (will still start with 2 though)
Update 13.02.2012
Made some minor progress on my project.
First of all, a friend of min is a classic Opel/Vauxhall enthousiast and he told me he has about 10 to 15 wiper motors lying around.
He's gonna scavage two of the same type so for now that's settled (hopefully they are powerfull enough).
Next I've mounted the Playseat GT in our attic with my xbox wheel on it for determining the optimal seating position:
(the computer in the back is one I got for free (Celeron D 2.66MHz) and has a serial port. This will be my Profiler system.
First thing I noticed is that the seat is quite upright and decided I wanted to tilt it backwards a litte.
So I made some simple aluminum bushes, wrapped in heatshrink to give them a nice black rubbery look:
at first I made the bushes in such length that I could still use the original bolts, but this didn't result in a large enough angle to my likings, so I bought some longer hex bolts and made the bushes about 2,5x longer.
This results in a comfortable seating position (sorry for the somewhat blurry pic):
Next step is finding the balance point, for this I informed at Fanatec what the CSR wheel, CSR elite pedals and CSR shifters wheigh, since that is the setup I'm planning to buy for the sim.
Guess I'll be using small beer crates instead of the pedals and wheel since a crate weight approx 1kg and a bottle about 0,5kg

Now let's hope YoBuddy's package will arrive soon as well as the components so I can start building and testing the AMC.
Update 08.02.2012
After a lot of reading and contact with YoBuddy (thx m8!) it is time to start a topic for my first Sim project.
Since it's my first project it'll most likely go paired with a lot of trial and error and thus I'm going to take my time for it which might result in less frequent updates, but I wanna do it right the first time.
As the title says, the project will be based on the Playseat GT which I bought at about half price and was used only once for a photoshoot:
I want to build a simple platform out of birch plywood (reckon 15 or 18mm) which holds the complete structure, here's a first rough sketch (top view):
The seat arrived yesterday and I'm working out orders for other hardware atm.
Fortunatelly YoBuddy had an unused Pololu Dual VNH2SP30 Motor Driver Carrier and a AMC 1.5~EZ v1.0 PCB lying around which he was willing to sell me for a very fair price. With that the controls are settled.
For the motors at first I have been looking at some cheap (€ 55,-) winch motors:
They do about 1A/7,5KG and since the Pololu driver can handle 14A/channel continuously this would result in a max continuous load per motor of 105Kg which should be more than enough.
Problem is that the supplier doesn't know the RPM of the motor only that they do 3.2m/min and thus I don't know if they are suitable.
For that reason I decided not to order them and go for wiper motors at first. Currently I'm still trying to find a matched pair of the right type that is usable (if anyone has any suggestions ......).
So far for the first post, I'll keep you updated!